Drop-In Lithium-Ion Battery Technology Mitigates the Risk of Explosion and Fire
A simple additive solidifies on impact for improved battery safety.
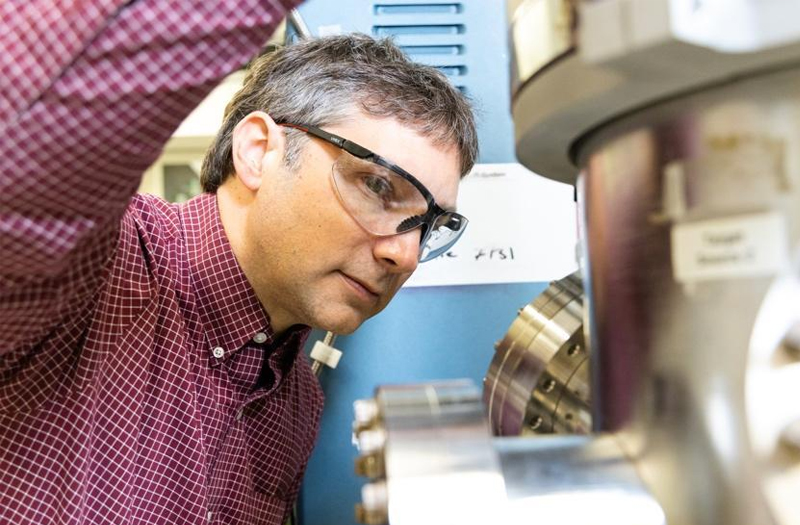
A gooey science experiment with his kids inspired Oak Ridge National Laboratory (ORNL) researcher Gabriel Veith to develop a new material that prevents lithium-ion batteries from bursting into flames.
ORNL scientists have been working for decades to expand the surprisingly complex foundational materials and chemical science behind batteries. In a lithium-ion battery, a thin piece of plastic separates the two electrodes–the points where electricity moves between parts of the battery. If the battery is damaged and the plastic layer fails, the electrodes can come into contact and cause the battery's liquid electrolyte to catch fire.
The eureka moment came when Veith and his kids were playing with a mix of cornstarch and water known as oobleck. “The mixture flows like a liquid until you start poking it, and then it becomes a solid,” Veith said. After the pressure is removed, the substance liquefies again. He realized this reversible behavior, known as shear thickening, could be exploited to make batteries safer.
Veith and his team set out to mix an oobleck-like additive into a conventional electrolyte to create an impact-resistant material. It solidifies when hit, preventing the electrodes from touching if the battery is damaged during a fall or crash. If the electrodes don’t touch each other, the battery doesn’t catch fire. Even better, incorporating the additive would require only minor adjustments to the conventional battery manufacturing process.
This characteristic depends on a colloid, which is a suspension of tiny, solid particles in a liquid. In the case of oobleck, the colloid consists of cornstarch particles suspended in water. For the battery colloid, Veith and his colleagues at ORNL and the University of Rochester used silica suspended in common liquid electrolytes for lithium-ion batteries. On impact, the silica particles clump together and block the flow of fluids and ions. The researchers used perfectly spherical, 200-nanometer-diameter particles of silica, or essentially a superfine sand.
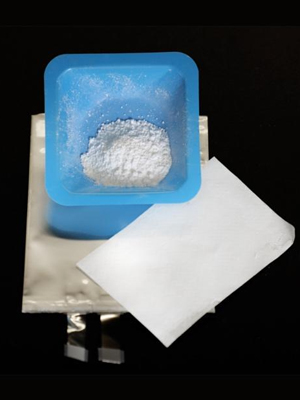
“If you have that very uniform particle size, the particles disperse homogeneously in the electrolyte, and it works wonderfully,” Veith said. “If they’re not homogeneously sized, then the liquid becomes less viscous on impact, and that’s bad.”
The team applied neutron scattering at ORNL’s Spallation Neutron Source, a Department of Energy (DOE) Office of Science user facility, to understand the fundamental interactions during impact.
“The best part of working at ORNL is the team environment. This team has a rheologist, a ceramicist, an electrochemist, mechanics experts, materials testers — all those together make this technology work,” Veith said. “This is not the work of a single person — teamwork allowed us this really unique opportunity. Having a diversity of people, experiences and backgrounds really helps to develop ideas.”
In 2022, ORNL licensed the collection of five patented technologies, called Safe Impact Resistant Electrolytes, or SAFIRE, to battery startup Safire Technology Group. The company recently expanded its R&D operations in Tennessee as part of its plan to commercialize the technology with an emphasis on applications in electric vehicles, defense, and electric vertical take-off and landing (eVTOL) aircraft.
“SAFIRE will transform the car industry, particularly as we pivot towards electric vehicles,” said John Lee, the company’s co-founder and chief executive officer. “The additive is easy to incorporate into existing battery-making processes and provides users with a safer alternative that is lighter and more effective than conventional battery protection, resulting in higher performance and lower total cost of ownership.”
The technology can significantly reduce vehicle weight and increase range by removing the need for heavy protective shielding around the battery. In defense applications, the technology provides projectile and ballistic protection while reducing the weight of defense systems and equipment.
“Improving battery technology is critical to building a clean energy future for our country,” said Susan Hubbard, ORNL deputy for science and technology. “This technology has implications for several industries, ultimately making battery systems safer, more efficient, and more stable.”
This article was created in partnership with Oak Ridge National Laboratory, learn more about their work.
Read more stories in the Basic2Breakthrough series.